深夜的农药制剂车间里,老王盯着离心机里残留的絮状物直摇头。这是本月第三次因杂质超标被客户退货,每次损失至少8万元。这个困扰行业多年的问题,正在被一种新型旋流梯度除杂装置改写结局。
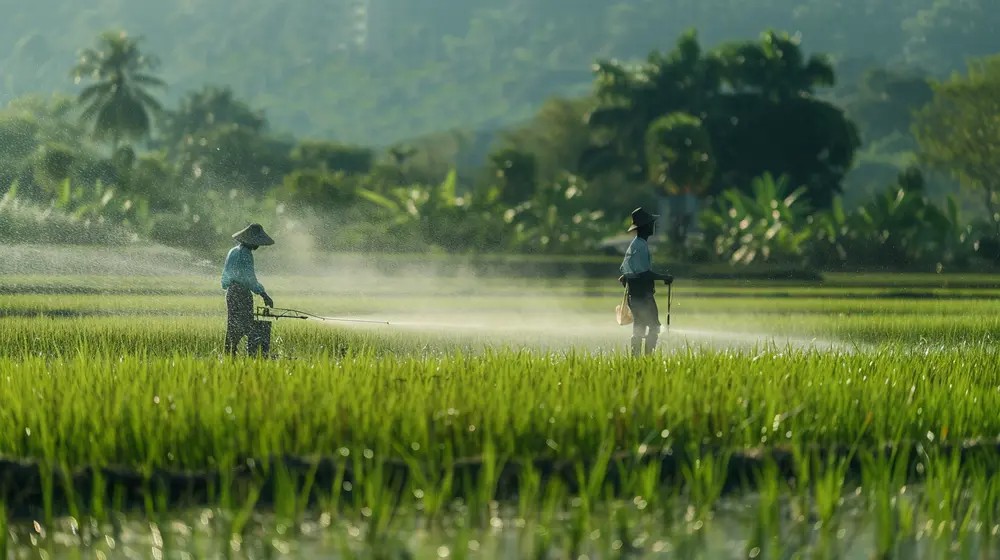
农药厂每年浪费的2000万去哪了?
某省农药协会数据显示,传统板框压滤机导致的有效成分流失率高达12%,按中型企业年产3万吨计算,相当于每年白扔2400吨原药。更严重的是,残留的胶体杂质会引发47%的批次稳定性问题——这些隐形成本往往被新手忽视。
三阶旋流技术如何实现零损耗?
与老式设备不同,蓝色新型装置采用密度梯度分离原理:
• 一级30μm旋流管拦截植物纤维
• 二级5μm陶瓷膜捕捉胶体颗粒
• 三级活性炭柱吸附色素杂质
实测数据显示,目标成分回收率从88%提升至99.2%,这意味着每吨乳油制剂可多赚取370元利润。
操作工必看的成本控制清单
在河北某农药厂实地考察时,设备主管老李掏出他的省钱秘籍:
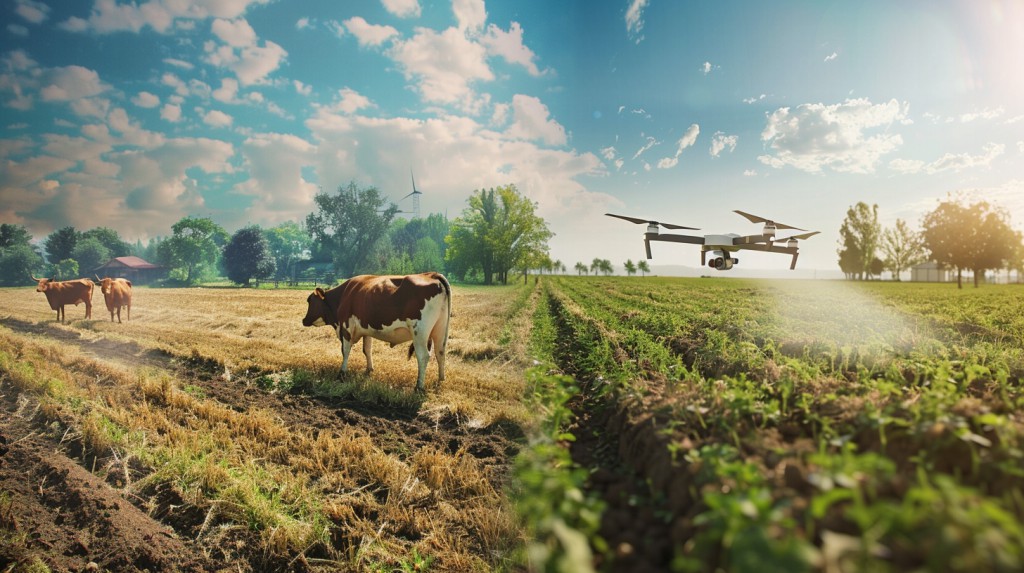
- 蒸汽消耗降低60%:预热系统改用余热回收装置
- 滤布支出归零:陶瓷膜组件寿命达12000小时
- 人工成本砍半:自动反冲洗功能减少3个巡检岗
"这套系统最妙的是处理粘度范围",老李摸着温控仪表说:"从水剂到悬浮剂,同一设备通吃8种剂型,不用像以前备三套机器。"
黑名单预警:采购时别踩这三个坑
去年震惊行业的"6·17溶剂超标事件",根源竟是供应商偷换了316L不锈钢材质。记住这些血泪教训:
• 材质证书要查钼元素含量(至少2.5%)
• 防爆认证必须包含丙酮蒸气项
• 梯度调节阀必须有物理刻度盘(纯数显易被篡改)
江苏某企业因忽略第三点,被列入供应商黑名单长达9个月。
未来农药厂的新风向
走访长三角产业带时发现,先行者已在尝试模块化设计——就像搭乐高一样组合不同精度的旋流单元。更令人兴奋的是某德企研发的AI预测系统,通过监测杂质光谱特征,可提前40分钟预警滤材堵塞,这项技术使武汉某厂意外停机次数下降了83%。
当被问及投资回报周期时,刚完成设备升级的浙江陈厂长算了笔账:"228万的设备投入,通过减少退货和降低损耗,14个月就回本了。"他办公室墙上挂着的杂质对比图,无声讲述着这场生产革命带来的蜕变。
