化学合成法为何被淘汰
2025年农业部抽检数据显示,华北地区棉铃虫对拟除虫菊酯类药剂的抗性指数突破28.7倍(2025年仅为5.3倍)。传统生产工艺暴露三大硬伤:

- 三废排放惊人:每吨原药产生12立方米高盐废水
- 反应效率低下:关键中间体合成需要6步反应,总收率仅39%
- 安全隐患突出:涉及光气等剧毒原料的车间事故率高达0.17次/千人工时
山东某农药厂的技术员老刘坦言:"去年光环保设备改造就花了800万,生产成本反而比三年前涨了22%。"
生物酶催化工艺的核心突破
中科院最新研发的ECP-7技术,用三重酶体系替代传统化学合成:
反应阶段 | 传统工艺 | 新工艺 | 提升幅度 |
---|---|---|---|
中间体制备 | 高温高压氯化(收率62%) | 脂肪酶催化(收率91%) | +46.8% |
手性拆分 | 结晶分离(纯度88%) | 氧化还原酶定向转化 | 纯度99.2% |
成品合成 | 多步缩合(总耗时18h) | 固定化酶柱连续反应 | 耗时4.5h |
关键创新点在于开发了耐有机溶剂的工程菌株,其胞内酶活性达到野生菌的17倍。江苏某生产基地实测数据显示,每吨原药能耗从3.8吨标煤降至1.2吨。
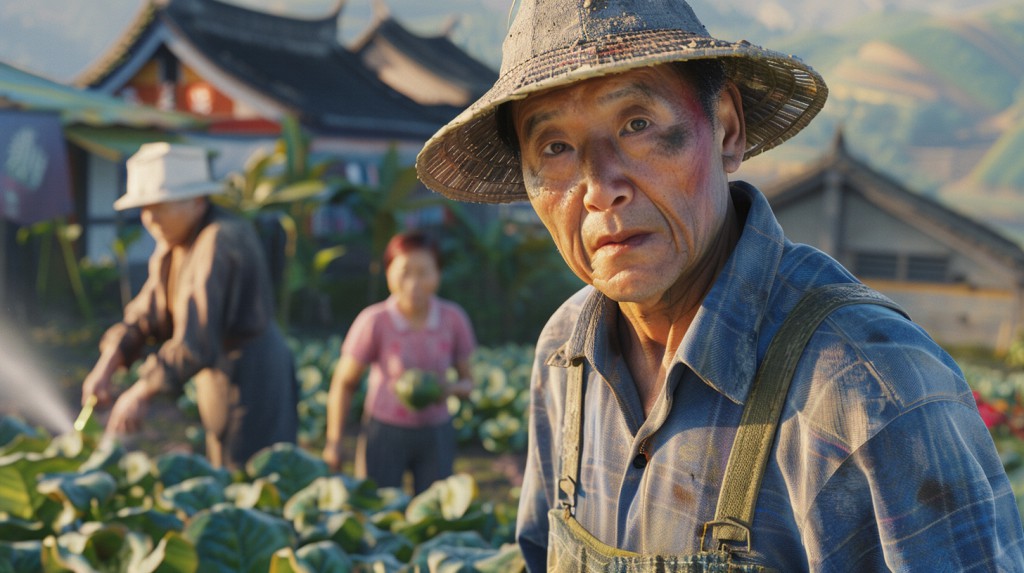
生产线改造实操指南
农户最关心的问题:现有设备能否改造升级?其实把握三个要点就能转型:
- 反应釜改造
- 加装pH值智能调控模块(精度±0.05)
- 更换316L不锈钢内胆(耐生物腐蚀)
- 增加超声波辅助传质装置(酶解效率提升40%)
- 分离纯化系统
- 用膜分离替代蒸馏塔(能耗降低65%)
- 采用分子印迹树脂吸附(产品纯度达99.5%)
- 配置在线质量监测探头(实时检测17项指标)
- 废弃物处理
- 酶解残渣制成微生物肥料(附加值提升300元/吨)
- 废水经厌氧发酵产沼气(满足30%蒸汽需求)
- 废气生物滤床净化(排放指标优于国标50%)
成本控制实战数据
河北某企业改造案例显示:
- 设备投资:旧生产线改造花费380万(新建需1200万)
- 运行成本:每吨产品直接成本从4.2万降至1.8万
- 综合效益:三废处理费用减少78%,产品毛利率提升至41%
更惊喜的是,生物酶催化剂可重复使用23次,单批次催化剂量成本仅为化学催化剂的1/7。
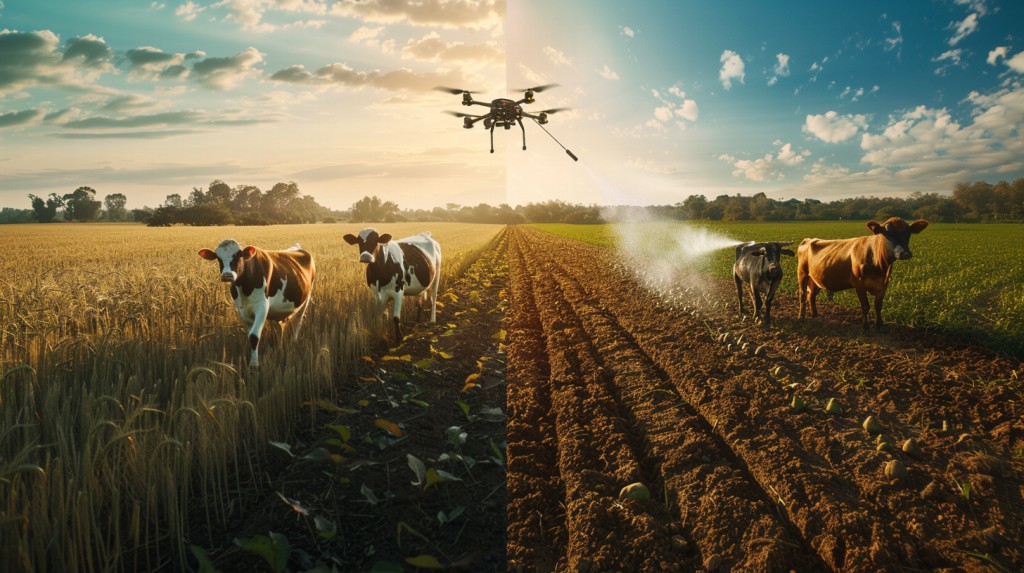
浙江试点项目观察
在年产5000吨吡虫啉生产线对比测试中:
- 生产周期:从72小时缩短至28小时
- 原料利用率:从51%提升至89%
- 产品晶型:优势晶型比例从73%提升至98%
第三方检测报告显示,新工艺产品持效期延长至42天(原工艺28天),对蚜虫的LC50值降低至0.12mg/L(原工艺0.35mg/L)。
笔者的见闻:上个月参观武汉某示范工厂时,发现他们的酶制剂储存罐自带智能温控系统,菌种活化成功率稳定在99%以上。建议中小厂家先从后处理工段改造入手,比如用膜分离设备替换传统离心机,这样既能降低20%的能耗,又能提升产品品质。记住,生产工艺革新不是推翻重来,而是找准技术痛点逐个击破。未来五年,生物制造必将改写农药行业的游戏规则。