为什么同样的乙草胺原药,加工厂产量能差出200公斤?
这个问题背后藏着农药行业的隐形利益链。一吨乙草胺原药的实际制剂产量,就像开盲盒——有人能产出1.9吨乳油,有人却卡在1.6吨。核心差异在于原药纯度检测误差、剂型适配度和工艺损耗控制。吉林某农药厂曾因采购标称97%纯度原药(实测仅94%),导致单吨损失3万元,这血淋淋的案例揭开了行业潜规则。
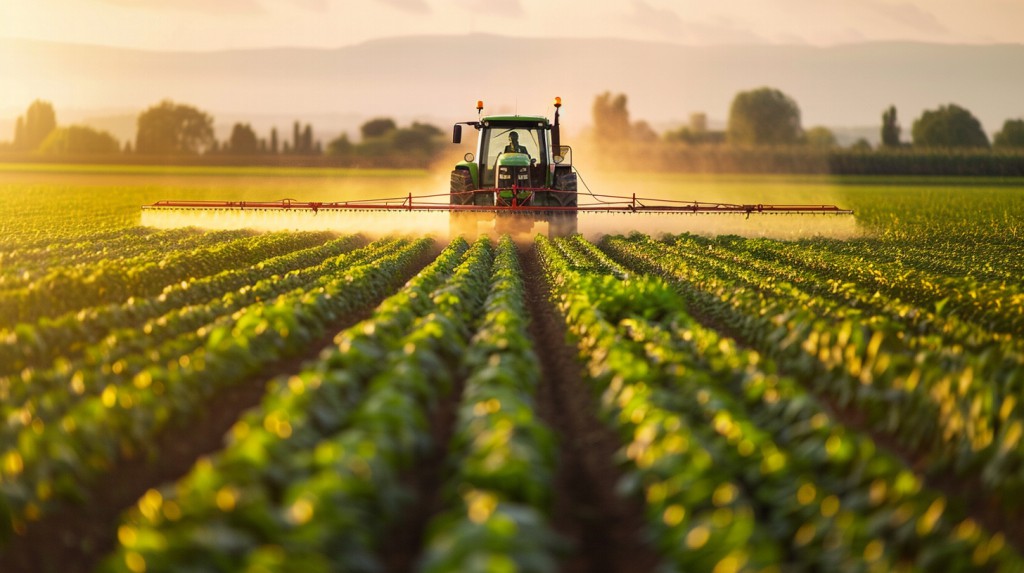
一、产量计算公式的三大变量
核心公式:实际产量=(实测纯度×1000kg)÷目标浓度×(1-实际损耗率)
- 乳油案例:实测95%纯度加工50%乳油,损耗率7%
→ 950kg ÷50% ×93% = 1767kg(约1.77吨) - 悬浮剂案例:实测92%纯度加工40%悬浮剂,损耗率10%
→ 920kg ÷40% ×90% = 2070kg(约2.07吨)
致命误区:
- 原药采购时忽略第三方检测(行业虚标纯度普遍达0.5-3%)
- 沿用传统醚法工艺(损耗率比甲叉法高4-6%)
- 错选剂型导致浓度适配偏差(乳油浓度误差超3%会引发药害)
二、三大剂型成本拆解与避坑清单
剂型 | 原药真实利用率 | 隐性成本陷阱 | 合规风险 |
---|---|---|---|
50%乳油 | 48-53% | 二甲苯涨价致成本波动30% | 欧盟禁用/国内环保督查 |
90%水分散粒剂 | 85-89% | 崩解剂进口依赖(价格年涨15%) | 东南亚海关新规检测壁垒 |
40%悬浮剂 | 36-40% | 砂磨机耗电成本(吨均增加200元) | 悬浮率不达标退货风险 |
真实案例:山东某厂2025年出口印尼的90%水分散粒剂,因崩解剂含量误差0.8%遭整柜退运,直接损失80万元。这提醒我们:国际订单必须预留2%质量冗余。

三、提产降耗三把斧
1. 原料端革命性突破
- 掺混精异丙甲草胺(价差5000元/吨,除草活性提升20%)
- 采购99%医用级原药(比农用级多产3%制剂)
2. 工艺端颠覆性升级
- 甲叉法连续化生产线(废水减排80%,获环保补贴3万元/百吨)
- 动态母液回收系统(实时回收3-5%跑冒滴漏)
3. 配方端创造性融合
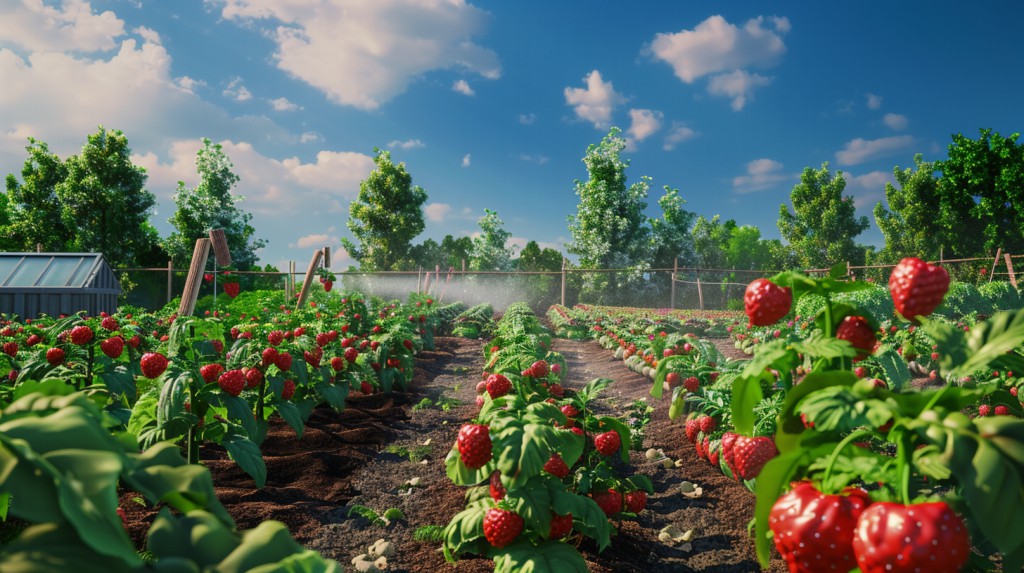
- 纳米微胶囊技术(药效延长至60天,亩用量减半)
- 四元复配体系(乙草胺+丙炔氟草胺+砜吡草唑+安全剂)
南通某企业引进德国动态回收设备后,单吨原药损耗从8%降至2.5%,年省成本超600万元。这验证了技术升级的投产回报周期仅需8个月。
四、2025年行业生存法则
价格预警:原药价格进入2.2-2.4万/吨平台期,但受阿根廷转基因大豆种植扩张刺激,南美市场需求量年增25%。
技术风口:
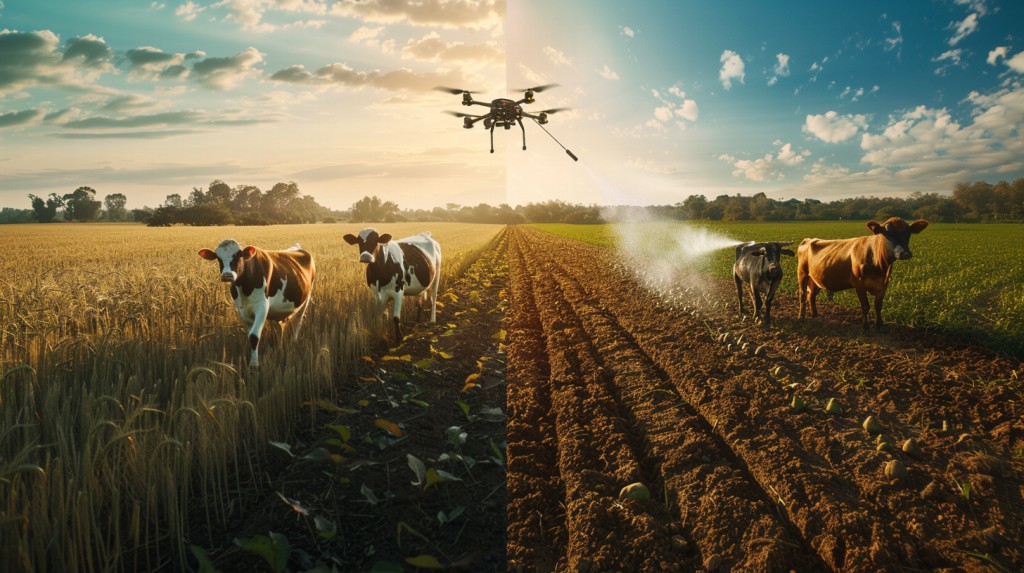
- 生物酶法合成工艺(能耗降低40%,纯度突破99.5%)
- 全水基化制剂技术(彻底摆脱有机溶剂依赖)
独家洞察:未来5年,乙草胺制剂将分化为两大阵营——传统乳油死守3元/亩成本红线,水基化悬浮剂抢占15元/亩高端市场。建议中小厂商主攻南美乳油代工,头部企业发力悬浮剂+AI施药系统集成方案。记住:在农药行业,活下来的不是最强者,而是最懂成本密码的玩家。